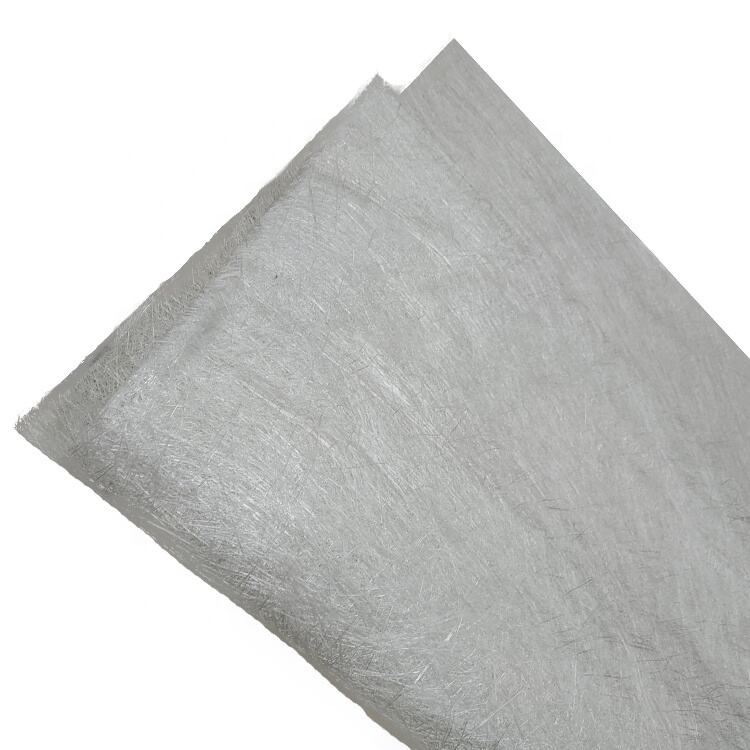
- Overview
- Inquiry
- Related Products
Key Features of Pultrusion Continuous Filament Mat (CFM)
Material Composition
Glass Fibers: Continuous filament mats are typically made from glass fibers, which offer high strength and excellent durability.
Filament Orientation: The fibers are laid out in a random or directional pattern depending on the specific application requirements.
Resin Compatibility: The mat is impregnated with a thermosetting resin (such as polyester, vinyl ester, or epoxy) during the pultrusion process to create a strong, rigid, and durable composite material.
Manufacturing Process
Continuous Fiber: In CFM, continuous strands of fiber are woven into a mat that is typically held together by a binder or stitching.
Impregnation with Resin: During pultrusion, the continuous filament mat is pulled through a resin bath, which saturates the fibers. The mat is then pulled through a heated die, where the resin hardens and forms the final composite shape.
Customization: The fiber orientation, type, and amount of resin can be adjusted depending on the mechanical and physical properties required for the end product.
Properties and Benefits
Strength-to-Weight Ratio: CFM offers an excellent strength-to-weight ratio due to the continuous glass fibers, making it a preferred reinforcement material in structural applications.
Corrosion Resistance: Glass fibers are highly resistant to corrosion, which makes pultruded composites ideal for use in harsh environments (e.g., marine, chemical processing, and outdoor applications).
Impact Resistance: Continuous filament mats provide excellent resistance to impact and abrasion, making them suitable for demanding structural applications.
Electrical Insulation: Glass fiber reinforced composites are non-conductive, which is an advantage in electrical and electronic applications.
Thermal Stability: The composites produced using continuous filament mats offer good thermal stability, particularly when using high-temperature resistant resins.
Applications
Construction and Infrastructure: Pultruded profiles are commonly used in building and construction, including for bridges, platforms, and structural beams.
Electrical and Electronic: The electrical insulating properties of glass fiber make it suitable for components like electrical boxes, cable trays, and support structures for power lines.
Marine: Used for boat hulls, decks, and other components exposed to marine environments due to its corrosion resistance.
Transportation: Used in manufacturing lightweight structural components for vehicles, such as buses, trucks, and railway cars.
Oil and Gas: In environments where corrosion resistance is critical, such as offshore platforms, pipelines, and equipment exposed to harsh chemicals.
Advantages of Pultrusion CFM in Manufacturing:
Consistency: The pultrusion process ensures uniform thickness and high-quality composite material throughout the profile.
High Production Rate: Pultrusion is a continuous process, allowing for high-volume production of parts, making it cost-effective for large-scale manufacturing.
Tailored Properties: The resin system, fiber content, and fiber orientation can be precisely controlled to tailor the final product’s mechanical properties (strength, stiffness, etc.) for specific applications.
Minimal Waste: As a continuous process, pultrusion generates minimal material waste, which contributes to more sustainable production.
Pultrusion Continuous Filament Mat (CFM) is a highly effective reinforcement material for creating high-performance composite profiles. It offers a combination of strength, corrosion resistance, electrical insulation, and thermal stability, making it ideal for a wide range of industries, from construction to marine and electrical applications. The versatility of CFM in the pultrusion process allows for the creation of complex shapes with consistent properties, ensuring that the final products meet the specific requirements of their intended applications.